GENERAL INFORMATION
All information about our products, such as our distribution area and our worldwide distribution partners, our usual delivery times, available packaging sizes and purity grades, can be found at the bottom of the page.In addition, there are hints and tips for storage and handling of photoresists and their auxiliaries. If not all your questions have been answered, you can always contact us.
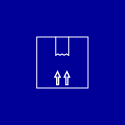
Our delivery time
Within Germany: 1-3 working days
On demand, in urgent cases our products can be shipped within 24 h to a destination inside Germany.
Usually, our shipments reach their destination in a few working days across Europe, and within 1-2 weeks in non-European countries. More information about lead times to other countries on request.
Notes: Since most shipments are dangerous good, we can not guarantee the duration of these shipments.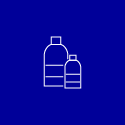
Our Sales Volumes
Our Photoresist
Beside original trading units (5 liters or 3.78 Liters) for production lines, for many of our resists we also offer small volume units (250ml, 500ml, 1000ml und 2500ml) rebottled in our clean room area class 10 in order to meet the demand of universities and research institutes.
In order to be able to optimally adapt your requirements to your order quantity, we have the above mentioned small containers in the program. If you yourself want to transfer the resist into smaller containers, we recommend a two-step cleaning process with first acetone and then isopropanol. Let the isopropanol evaporate completely from the bottle before you fill the resist. We also offer suitable empty bottles. Further information can be found here:
Our Ancillaries
Most of our ancillaries, such as etching mixtures, solvents, acids, bases and strippers, are supplied as standard in 2.5 liter or 5 liter containers. Other available sales units (1 liter, 30 liters, 60 liters, 120 liters and 200 liters) are directly in our shop or can be requested with us.
> Technical data of our bottles
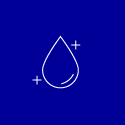
Purity Grade
The reasonable purity degree of process chemicals depends – among many other parameters – on the minimum feature size to be realized, the required yield, the cleanroom class and subsequent process steps.It is almost impossible to definitely correlate suboptimum process results with a purity degree of the chemicals applied being too low. Therefore, one cannot make a definitive statement on the required purity grade. With VLSI and ULSI qualities, we fulfil almost all requirements in research and development as well as in production. In our booklet “Our Products” (available on request!), we introduce our resists, solvents and etchants with their available purity degree(s).
MOS (metal oxide semiconductor)
Impurity metal ion concentration (per element) approx. 100 ppb, particle concentration < 1000/ml
VLSI (very large scale integration)
Impurity metal ion concentration (per element) approx. 10-50 ppb, particle concentration < 250/ml
ULSI (ultra large scale integration)
Impurity metal ion concentration (per element) approx. 10 ppb, particle concentration < 30 ... 100/ml
SLSI (super large scale integration)
Impurity metal ion concentration (per element) approx. 1 ppb, particle concentration < 30 ... 100/ml
PPM, PPB and PPT
1 ppm (parts per million, 10-6) corresponds approximately to one drop (approx. 30 µl) in a rather large bucket.
1 ppb (parts per billion, 10-9) corresponds to one drop in a comparably small swimming-pool.
1 ppt (parts per trillion, 10-12) would be one drop in a small lake, or a 5 µm particle dissolved in a cup of coffee, or approx. 100,000 atoms in a drop!
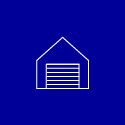
Storage and handling of photoresists and ancillaries
Expiration date
The meaning of the expiration date
From the time of production, all chemicals are subjected to an ageing process where the composition of the product changes steadily. In the case of photoresists, this can mean the decomposition of the photo-active substances, in the case of negative resists, the cross-linking reactions of the resin and, in the case of developers, the neutralisation due to the penetration of CO2 through the container walls. In addition, particles and metal ions can dissolve in the product affecting the degree of purity.
By specifying the expiration date, the manufacturer specifies how long, under the specified storage conditions, the specifications of the product can be maintained with regard to its composition, its properties during processing and its degree of purity.
Process management before and after expiry of the expiration date
Because in all ageing processes, continuous changes occur in the product properties, the expiration date does not mean that a product can be used until the expiration date unchanged and after the expiration date can no longer be used. Rather, in the case of very critical processes with narrow parameter windows, or processes running at the edge of the optimum parameter window, it may be necessary to readjust certain
parameters, such as the exposure dose or the development time, before the end of the expiration date.
Very uncritical processes, on the other hand, can make it technically possible to use products far beyond the stated expiration date without any significant effect on the result.
Temperature ranges during storage
Storage temperature and ageing
The specified expiration date always refers to a specific temperature range during storage. Exceeding temperatures may cause certain parameters to be
outside of the prescribed specifications prior to the end of the nominal shelf life. Cool temperatures, on the other hand, can slow the ageing process and thus slow the drift of the process parameters.
Photoresists
The effects on high storage temperatures of photoresists correspond to accelerated ageing. In the case of non-critical resists or/and processes with a wide parameter window, storage at room temperature is usually justifiable.
In the case of critical processes, particularly heat-sensitive photoresists or the requirement of being able to use the resist beyond the nominal expiration date, a strong> storage temperature of 5 - 10°C should be aimed for (unless the manufacturer specifies lower temperatures). Chilled containers must be adjusted to the ambient temperature before opening (e.g. taken out of the refrigerator the evening before processing) in order to prevent the formation of condensation in the resist bottle, which can damage the resist. In the case of continuous consumption, it can therefore be useful to store a separate filling in a smaller container at room temperature and to consume it while the larger original container is stored in a cooled manner.
Developer and remover
In the case of aqueous developer solutions, only freezing should be prevented, while a moderate and not long-term exceeding of the recommended storage temperature does not generally adversely affect the product properties.
Cold-sensitive products
The solvent DMSO (dimethyl sulfoxide) has a melting point just below room temperature, so it can possibly freeze in storage in cooler rooms. Thawing may require several days, but the product can still be used as it is.
Buffered hydrofluoric acid (BOE) crystallises in a cool environment, depending on the HF concentration. Here, too, use is possible to use the BOE after thawing. However, because of the small crystals still present days later, which can settle on the substrate, care has to be taken.
Ageing of photoresists: Effects
Particle formation
DNQ-based positive and image reversal resists tend to gradually form particles when strongly diluted. After the coating, the naked eye shows a rough resist surface until the resist becomes progressively inhomogeneous (strong ripple, resist cracking behind larger particles) in a later stage.
Some low-viscous and photoinitiator-rich thin resists such as the AZ® 1500 series are significantly more affected by this ageing phenomenon than thick resists.
Since the resist is missing the photoinitiator due to its deposition, the development rate decreases or the dark erosion increases during the development, which is why a filtration of the photoresist with the
particles formed does not lead to the same result as a fresh photoresist.
Loss of the photoinitiator in positive resists
The photoinitiator of positive, image reversal and some negative resists also gradually decomposes at the recommended storage temperature over
months and years.
In the case of positive resists, this loss of photoinitiator means a lower rate of development and a higher dark erosion (because an unexposed photoinitiator as an inhibitor reduces the alkaline solubility), thus a lower contrast. Not only does the structural integrity and sidewall slope of the developed structures suffer, but also narrow structures are harder and harder to open. The N2 released from the photoinitiator dissolves in the resist and can form bubbles during coating when the resist bottle has been closed for an extended period of time and the N2 has thus been allowed to accumulate.
With image reversal resists in the negative mode and negative resists, the image reversal or cross-linking is less pronounced with a lower concentration of photoinitiator, causing the exposed resist areas are more vulnerable to the developer. The resist structures can thereby change in various ways: With image reversal and negative resists which are completely exposed up to the substrate, vertical or undercut resist sidewalls are increasingly positive due to the greater degradation by the developer. In the case of weakly exposed image reversal and negative resists, the reverse reaction or cross-linking especially close to the substrate can be so weak, that the erosion of the resist in the developer is increased and can cause the separation of smaller or narrower structures in the developer.
Cross-linking reactions with negative resists
In expired negative and image reversal resists (e.g. the AZ® 5214E), the cross-linking agents present may begin to cross-link the resin during storage, thereby decreasing the development rate of the unexposed negative resist or flood-exposed image reversal resist.
Not only does the structural integrity and sidewall slope of the developed structures suffer, but also narrow structures are harder and harder to open. The partial cross-linking of the resin reduces the
removability of the resist film at the end of the litho process: In expired AZ® 5214E, difficult to dissolve residues can be detected after stripping.
Discolouration
In the case of a batch change of positive and image reversal resists, a different (usually brighter) colour of the new resist is occasionally apparent. The gradual darkening of the photoresist is due to the formation of highly absorbing dyes through the esterification of the photoinitiator with the resin but has no significant effect on the processing and performance of the
resist: Already minimal traces of such converted photoinitiators strongly dye the resist in the visible range, which does not however significantly affect the UV absorption which is decisive for the exposure.
Resist adhesion
A resist adhesion loss which can take place in case of expired resists is based on gradual chemical changes of the resin, which can be compensated within limits in some processes via optimised substrate pretreatment and / or a hardbake.
Because other ageing phenomena of the resist are also likely to worsen the litho result at this stage, the use of a fresher resist batch is
recommended in the case of an adhesion deterioration caused by resist ageing.
Viscosity
A small amount of the solvent evaporates when resist containers are opened. Already 1% solvent loss significantly increases the viscosity and therefore the film thickness attained by spin coating. As a result, the exposure doses necessary for an exposure and subsequent complete development can be increased. Due to the low vapour pressure of the commonly used solvents, however, this effect only occurs theoretically after several 100 bottle openings, each with a complete exchange of the solvent atmosphere therein, and can even be compensated in this case by means of higher spin speeds during spin coating.
Developer: Ageing and development rate
Neutralisation through CO2
The ageing aqueous alkaline, NaOH, KOH or TMAH-based developer is based on CO2 absorption from the air, which decreases the rate of development. Therefore we recommend storage in well closed original containers.
In open developer baths, a N2 curtain minimises the CO2 intake. Without such a N2 barrier, the shelf life of a developer basin depends primarily on the ratio of the surface area of the developer to its volume which is why the activity of small (L-sized) developer beakers can already be reduced after a few hours.
The CO2 insertion, due to the dead volume of a developer container that is exposed to air when a container is opened, can usually be disregarded: Approx. 1.7·10-5 mol/L CO2 of air are approx. 0.25 mol/L OH-ions which are neutralized by the CO2 only with very frequent opening of the container and / or a very small residual volume of the developer.
Chemical buffer
Some developers (such as AZ® 400 K, AZ® 351 B) contain chemical buffers, which reduce the decrease of the pH value through the CO2 insertion achieving a constant long-term development rate - compared to
pure NaOH/KOH batches. The exhaustion of the developer by the development process itself is not stopped.