PHOTORESIST PROCESSING FOR ELECTROPLATING
Optimally suitable photoresists
Acid and alkaline resistance of the resist mask
The phenol and acrylic resins used as the resist matrix for all common AZ® and TI resists make these photoresists largely stable in acidic electroplating baths, as long as they are not strongly oxidising media such as nitric acid. Alkaline baths, on the other hand, can attack a non-crosslinked (positive) resist mask from a pH value of around 10 during electrochemical deposition, whereby the resist damage or infiltration depends on the temperature and duration . It should be noted that the pH value measured in the bath does not necessarily correspond to the at the site of metal deposition (and therefore at the site of the paint structures) . A hardbake can only increase the alkaline resistance of positive enamels at temperatures of approx. 140°C and above. These are above the softening point of all positive lacquers, which means that the lacquer profiles are rounded after such a hardbake and are therefore usually no longer suitable for electroplating.
Crosslinking negative enamels such as AZ® nLOF 2000, AZ® 15 nXT or AZ® 125 nXT have a significantly higher alkaline stability compared to positive enamels.
Resist adhesion to the substrate
Due to the swelling of photoresist, the adhesion to the substrate can decrease during the electroforming process and metal can infiltrate the resist layer and thus grow underneath it. The resist adhesion can be optimised via the resist selection, its processing and the substrate pre-treatment . The AZ® 1500, 4500, 10XT and ECI 3000 lacquer series show fundamentally improved adhesion to the substrate compared to lacquers optimised for dry chemical processes. Crosslinking negative varnishes such as the AZ® nLOF 2000 series or the AZ® 15 nXT or AZ® 125 nXT also exhibit very good adhesion.
Optimisation of paint adhesion
Adhesive layer
In principle, a thin metal film is highly recommended as an adhesion promoter, especially for applications in electroplating, as a metallic seed layer is required in many cases anyway: A few nm thin titanium or chrome film significantly improves paint adhesion, especially in comparison with gold or platinum. Such a thin metal film can - if necessary - be removed after development on the freely developed areas in suitable media. Care must be taken here to ensure that is not etched too much laterally under the resist film, i.e. the etching process does not take much longer than it takes to remove the freely developed metal layer.
Softbake and hardbake
Optimum softbake parameters (for most standard lacquers we recommend 100°C for one minute per µm of lacquer layer thickness on the hotplate, a few minutes longer for oven processes) also improve lacquer adhesion. It is important, especially for thick resist layers, to avoid abrupt cooling of the substrate after the softbake in order to prevent cracking in the photoresist layer. Although a baking step after development can improve the resist adhesion, in the case of positive resists the temperatures of 120-140°C required for this are usually above the softening point of the resist used, which causes the resist structures to round off. With negative lacquers, such a hardbake can be carried out without the risk of rounding the lacquer profile. However, the later removability of the resist mask in wet-chemical media decreases with increasing hardbake temperature.
Residual solvent
Photoresist layers dried under standard softbake parameters still have a residual solvent content of a few per cent. If the solvent enters the bath during electroplating, this contamination can disrupt the chemistry of the deposition. In this case, a more intensive (i.e. longer or hotter) softbake is recommended at . In the case of thick resist layers, where even a long softbake leaves a relatively high residual solvent content near the substrate , a baking step after development can be helpful. In order to preserve the resist edges when using positive resists, this should be carried out at a maximum of 20 °C below the softening temperature of the photoresist used. With cross-linked negative resists, there is no need to fear any subsequent rounding of the resist structures, although the removability of the resist mask after electroplating decreases if the baking temperatures are too high.
Optimisation of the adhesion of the deposited metal
Development
If the photoresist is developed with an unsuitable developer or is not rinsed sufficiently after development, a few nm of thin, difficult-to-detect resist residue can prevent optimum growth of the deposited metal. If such resist residues appear despite sufficiently long development and subsequent rinsing, the use of the developer AZ® 2026 MIF (either as a replacement for a previously used developer or as approx. 30 second dip after the actual development) can provide a remedy with its additive .
Adhesion promoter
Incorrectly applied adhesion promoters, such as liquid HMDS, can also reduce the adhesion of the grown metal to the seed layer. Organometallic adhesion promoters such as TI PRIME can also impair the adhesion of the grown metal, if they are not removed in the freely developed areas, e.g. by an HF dip.
Lacquer profile
Vertical edges
If vertical edges are required, the AZ® ECI 3000 positive resists are recommended for photoresist masks just a few µm thick, while the AZ® 4562 or AZ® 10XT positive resists or the AZ® 15 nXT negative resist are also recommended for 5 - 30 µm thick layers. The positive AZ® 40 XT or the negative lacquer AZ® 125 nXT can be used for very thick layers of 30 - 150 µm with very steep edges.
Negative edges
If the moulded metal structure is to have a positive profile, the AZ® nLOF 2000 negative lacquer series is recommended as a lacquer mask for layer thicknesses up to approx. 20 µm, and the AZ® 15 nXT negative lacquer for even greater layer thicknesses. With both resists, the shape of the undercut can be adjusted over a wide range via the exposure dose and the post exposure bake.
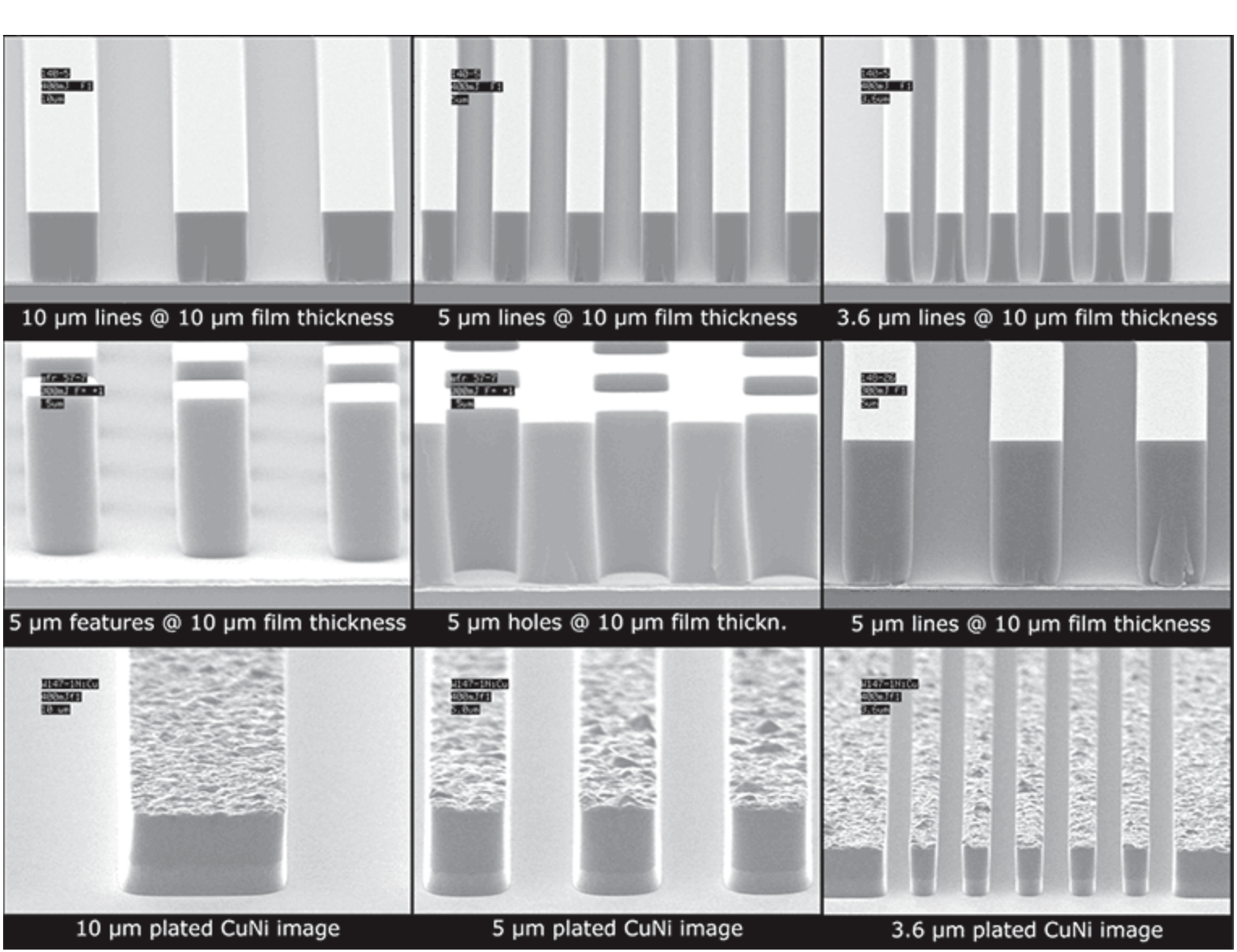
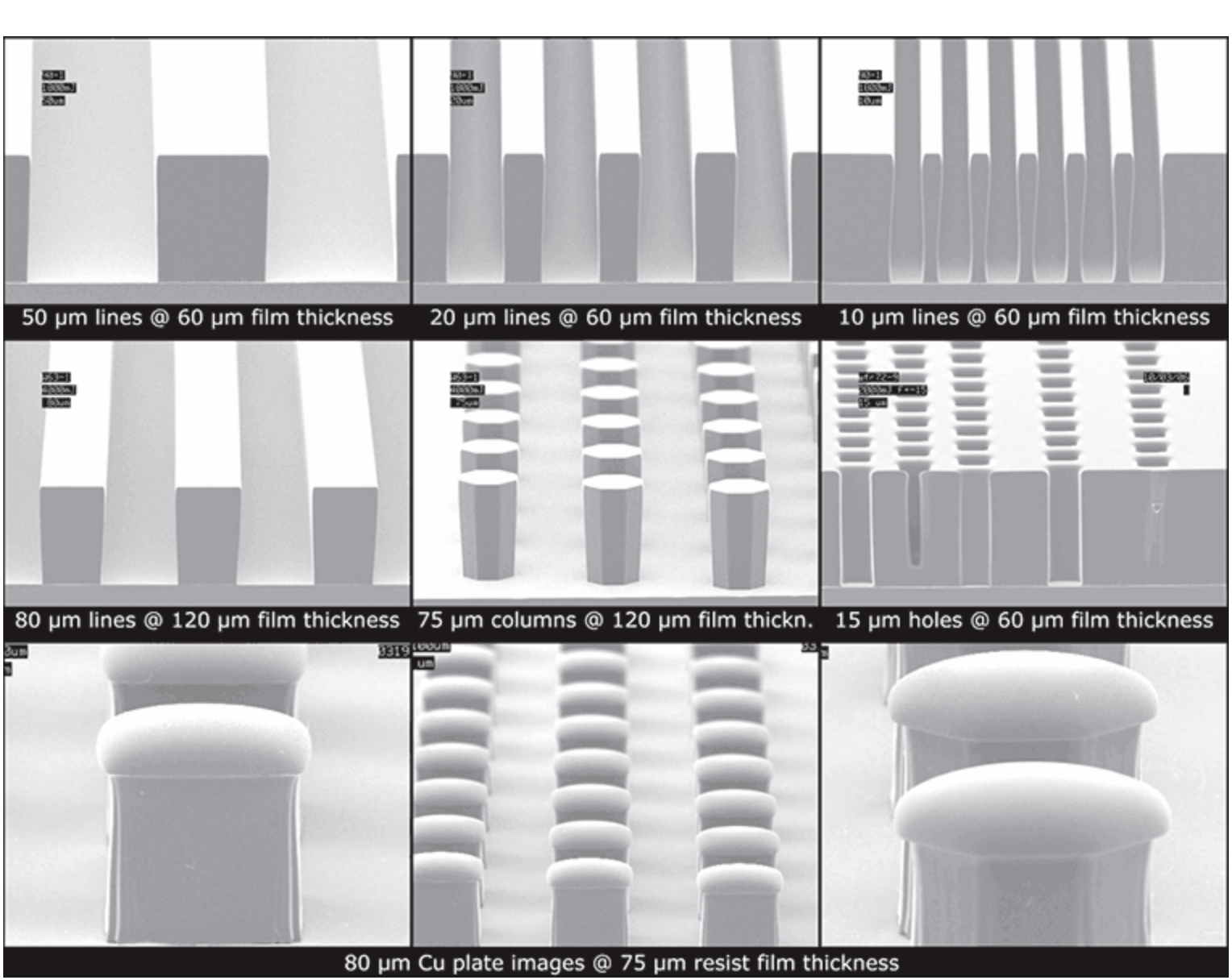