AZ ECI 3012 Photoresist - 3.785 l
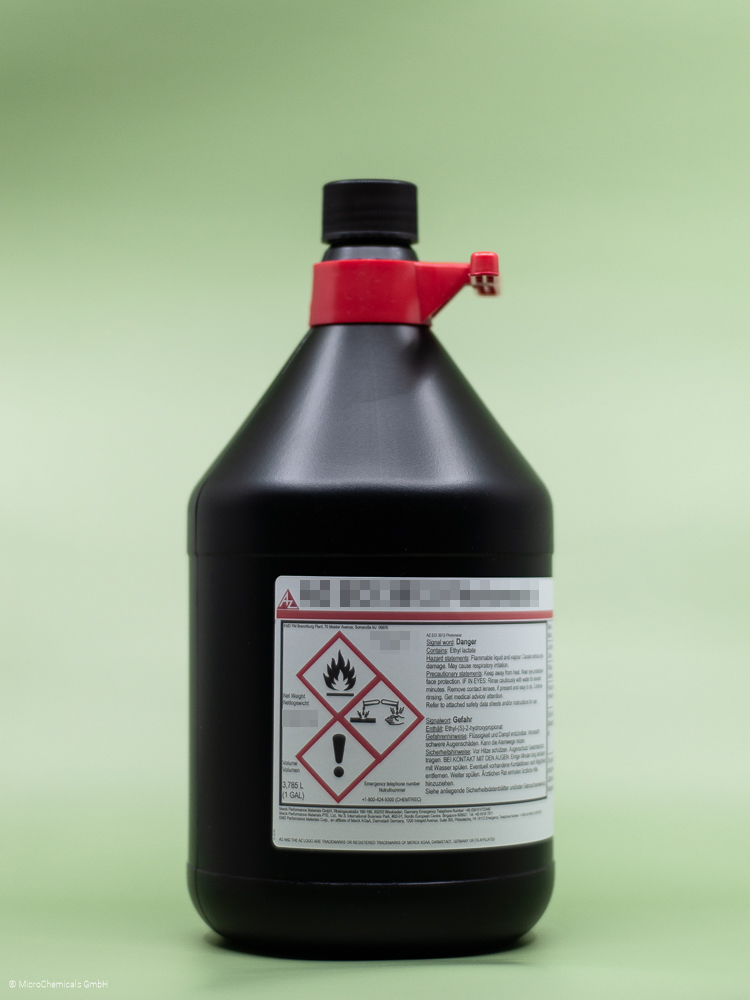
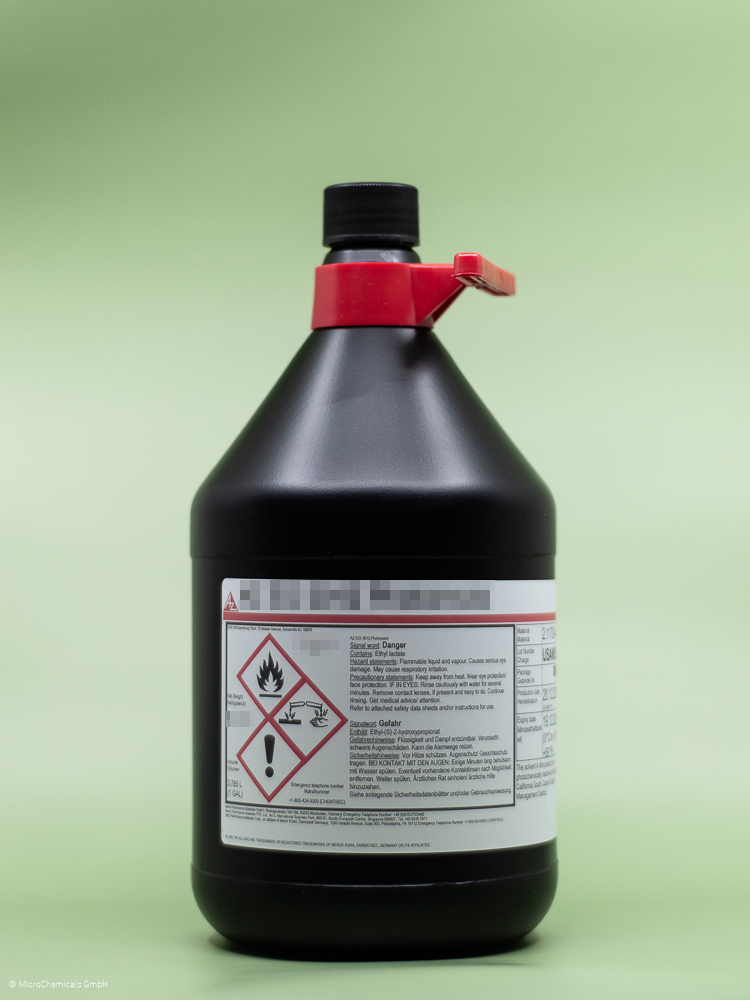
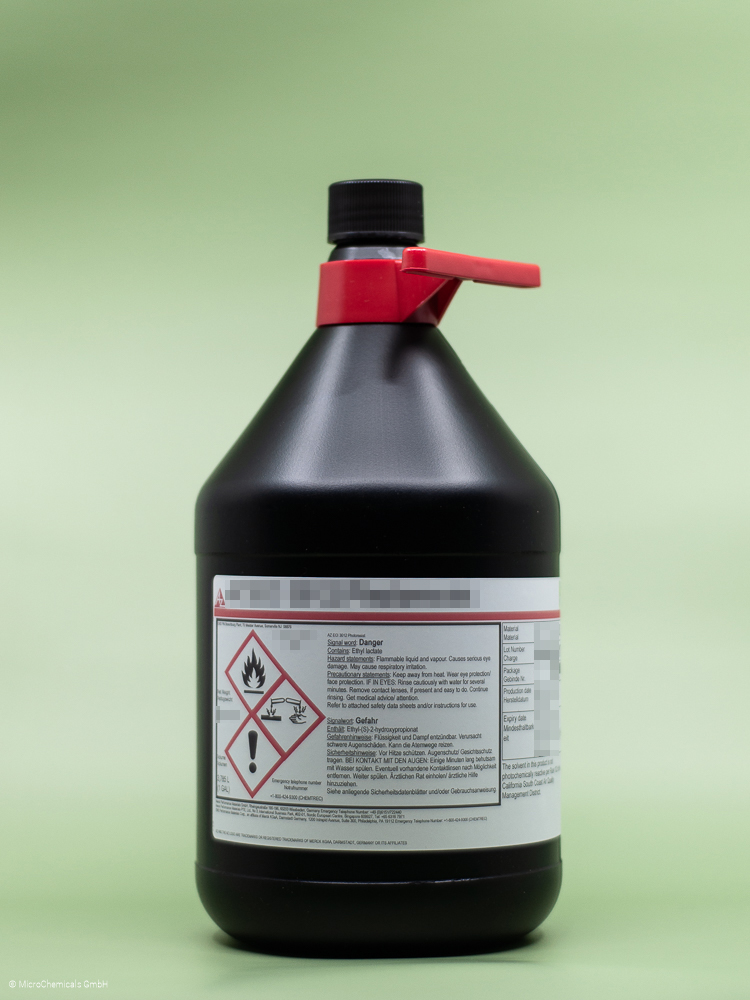
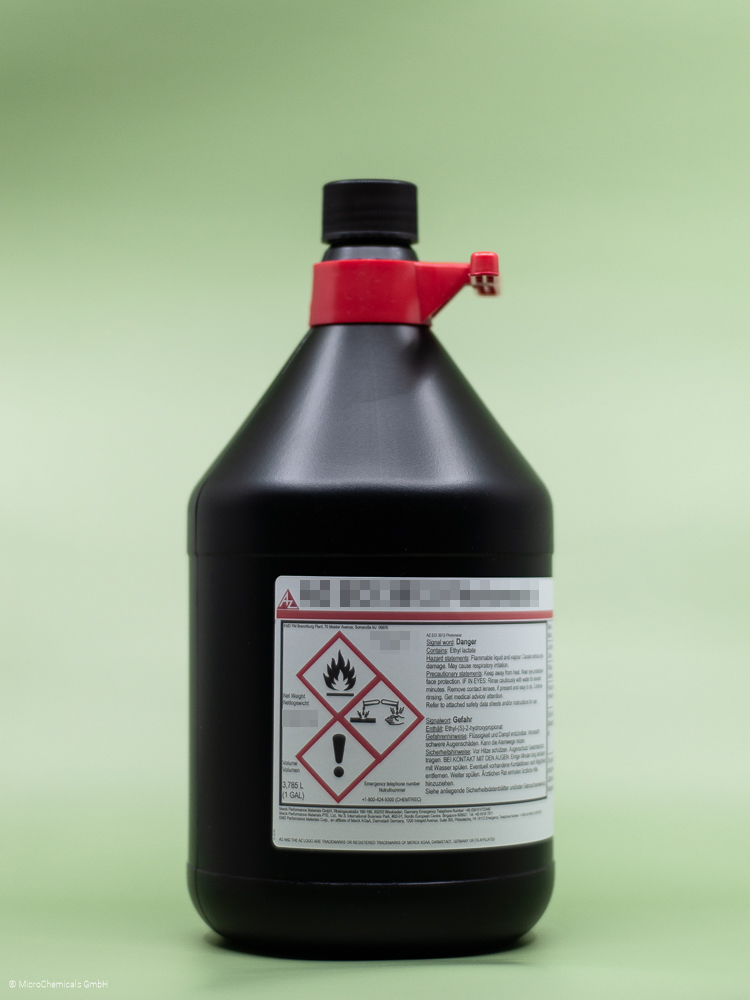
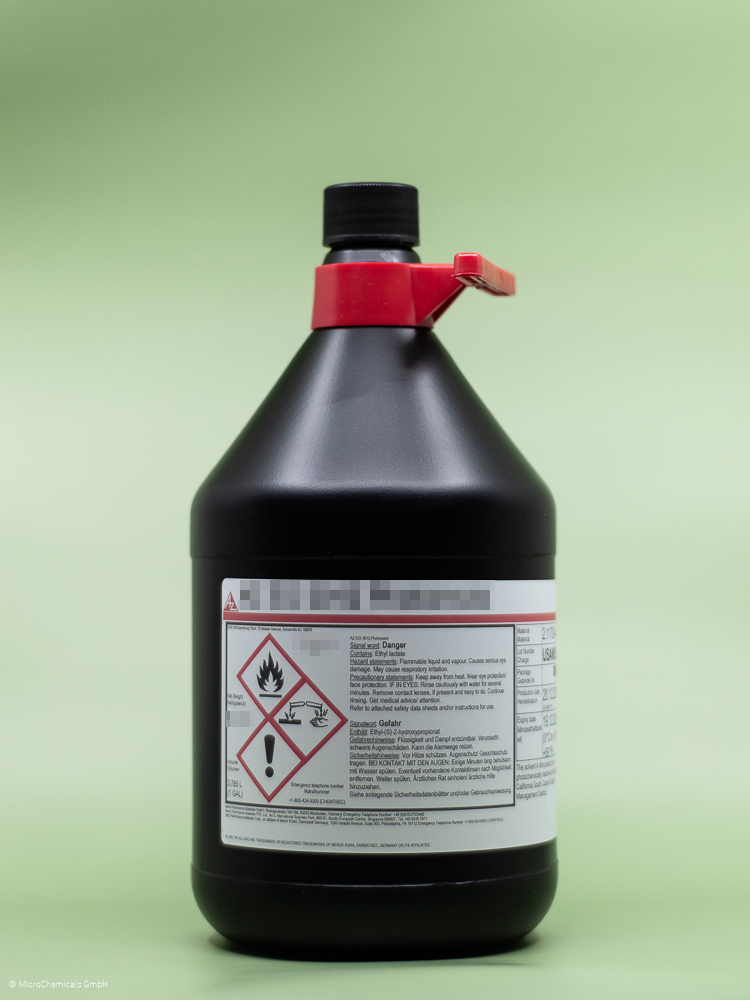
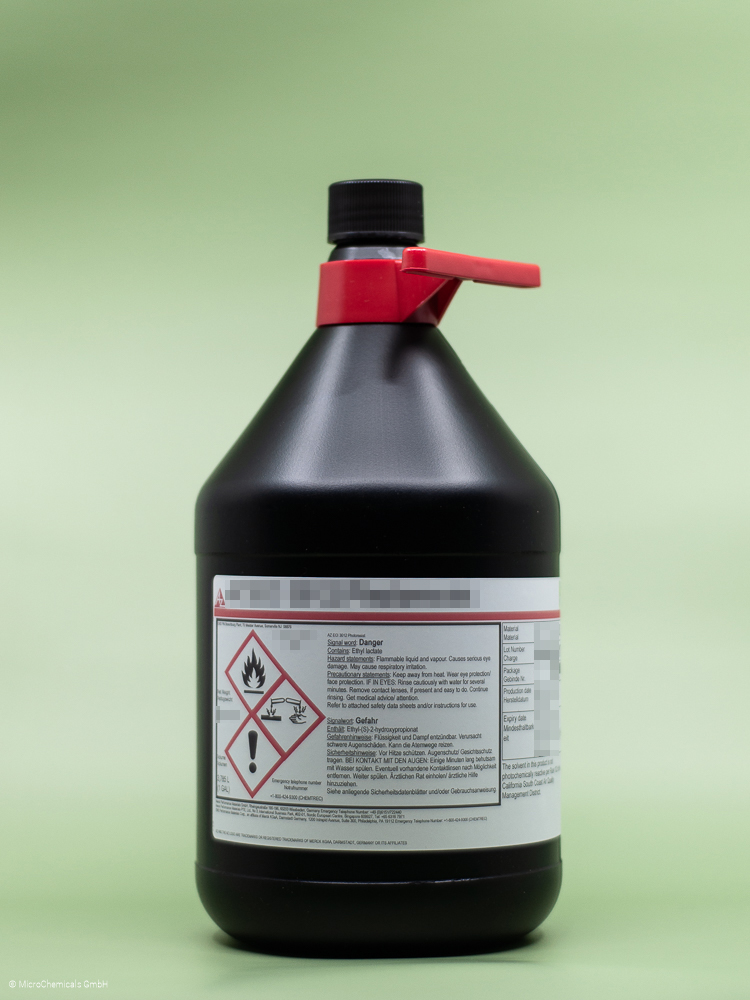
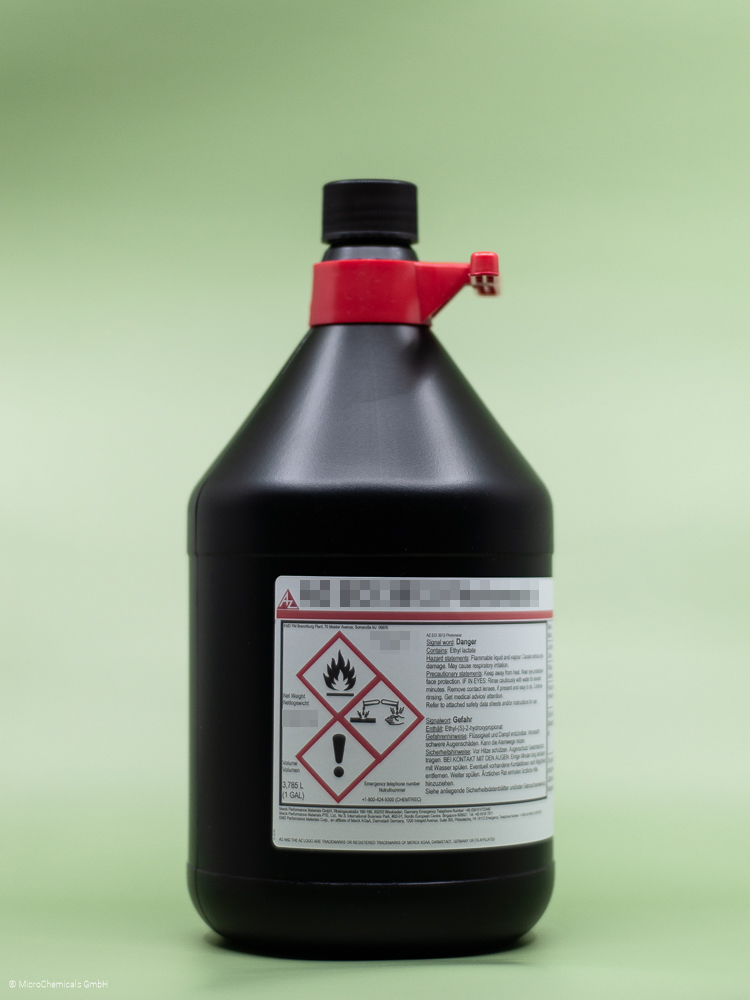
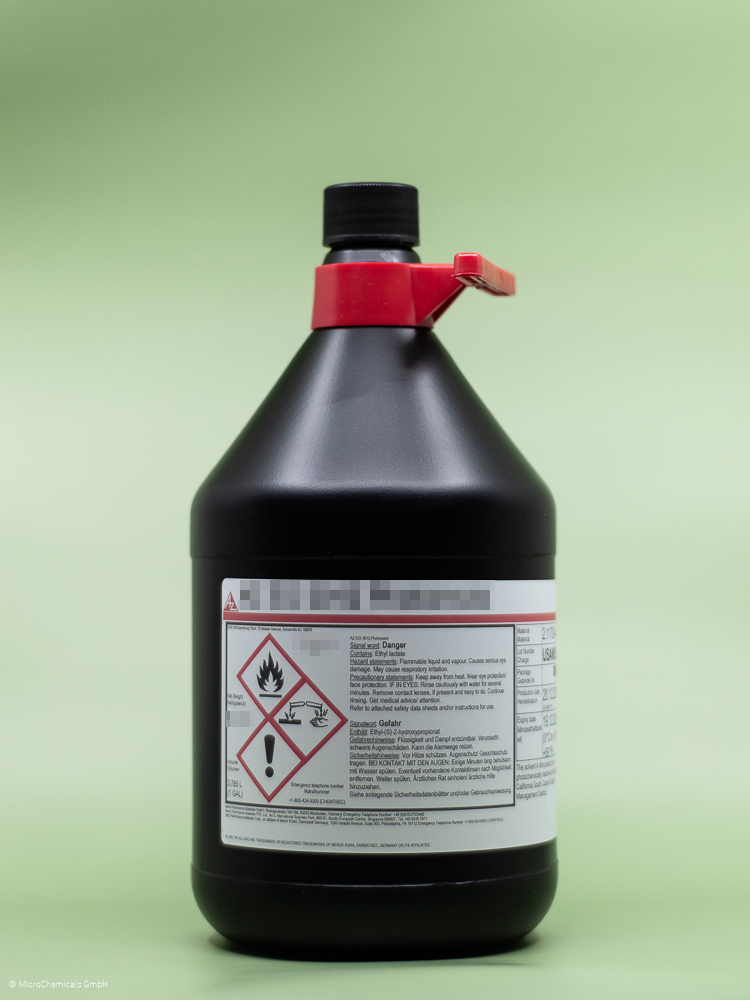
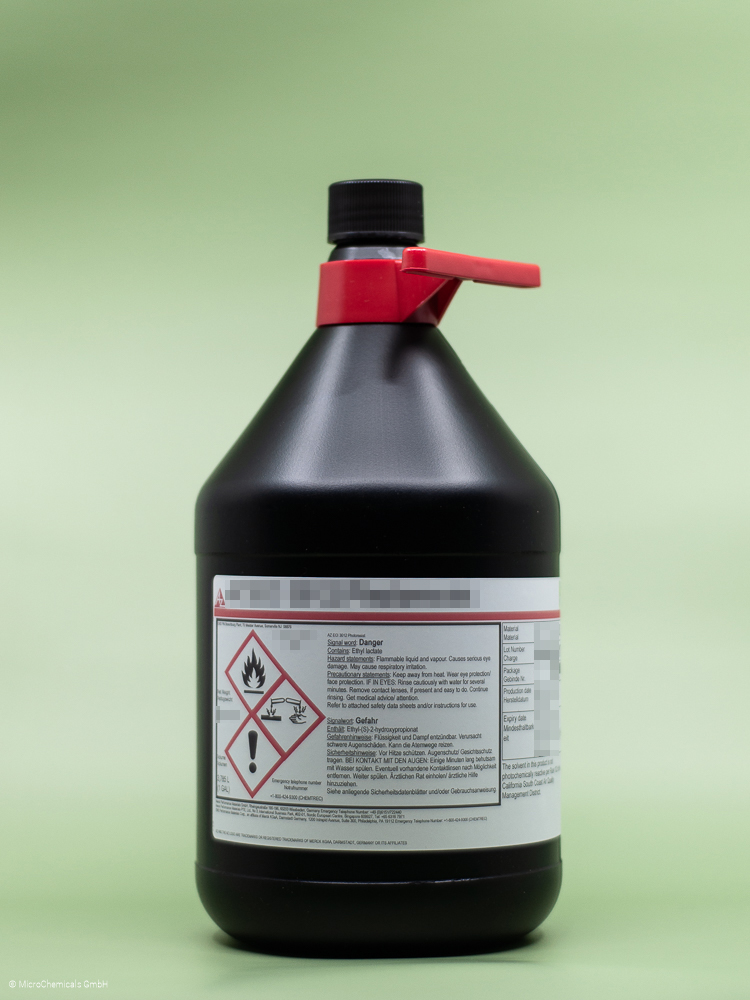
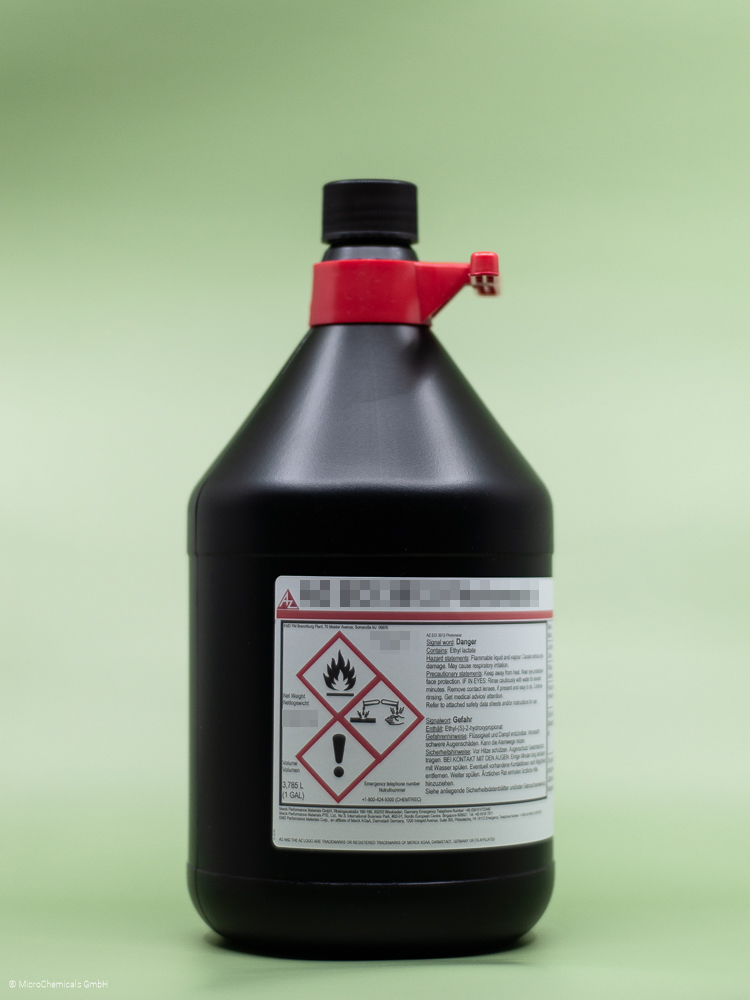
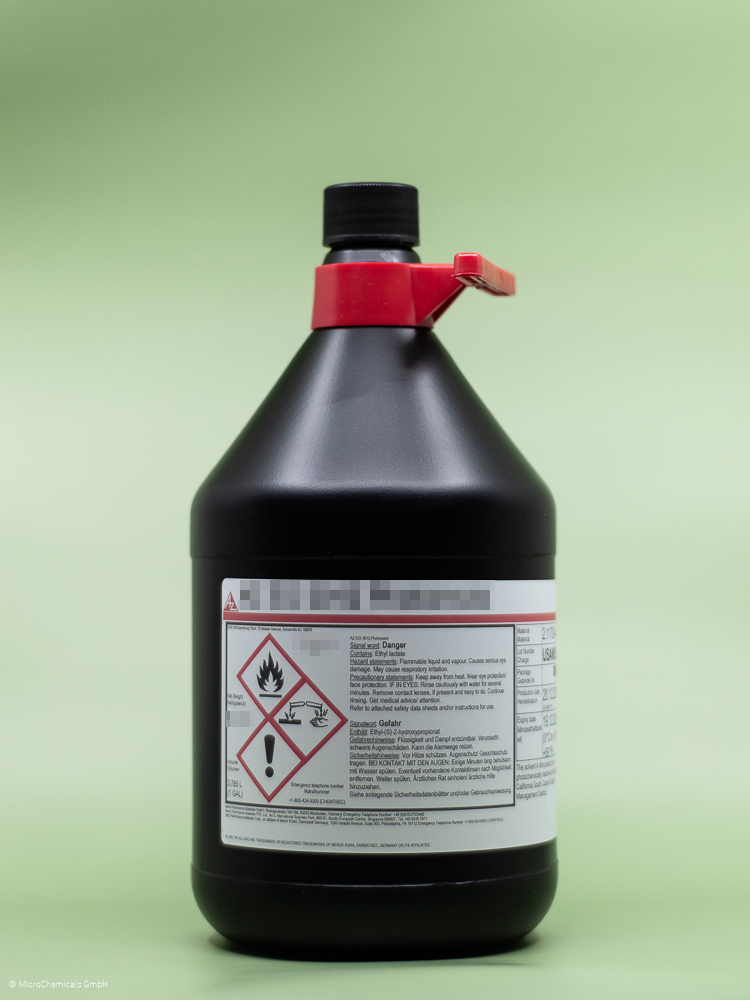
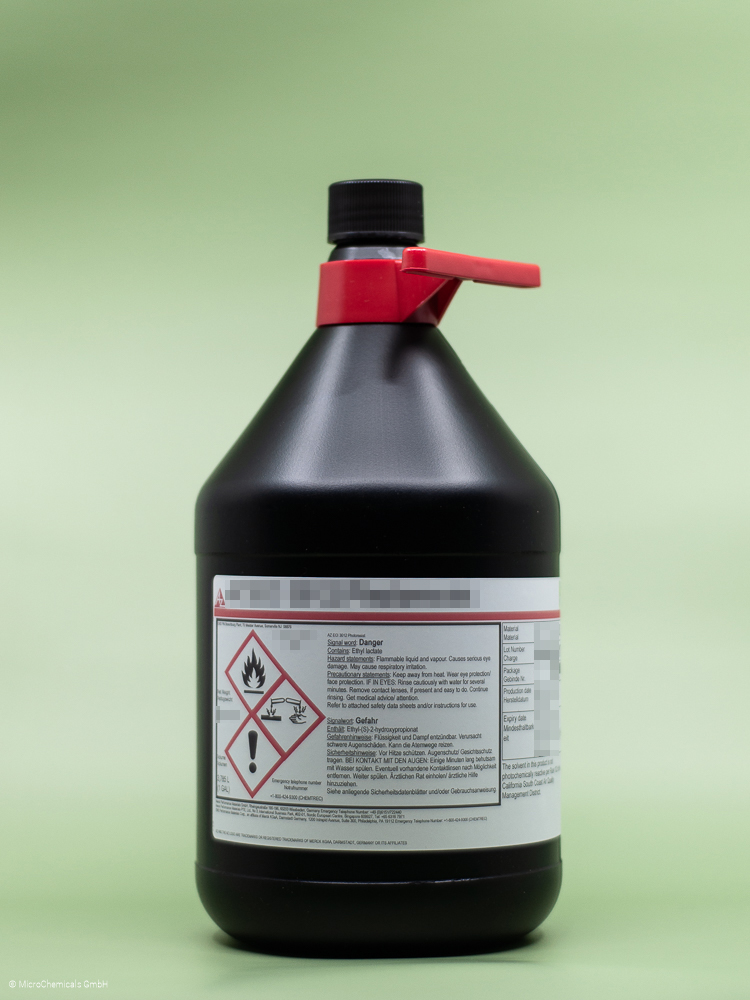
Product information "AZ ECI 3012 Photoresist - 3.785 l"
AZ® ECI 3012
High Resolution with Broad Process Window
General Information
AZ® ECI 3012 belongs to the AZ® ECI 3000 series of positive thin resists (g-, h- and i-line sensitive), whose main applications are as a resist mask for dry etching, RIE, ion implantation or lift-off processes.
450 nm resist lines with the AZ® ECI 3012 at approx. 1.2 µm film thickness.
Product Properties
AZ® ECI 3000 resist family is optimized for steep resist sidewalls and high stability against thermal softening (softening temperature approx. 125 °C). AZ® ECI 3000 resists require a significantly lower exposure dose compared to other positive resists, but still develop quickly. AZ® ECI 3012 covers the resist film thickness range of approx. 1.3 µm at 3000 rpm with adapted spin profiles. This resist is often used for dry etching, RIE or lift-off processes and allows a resolution in the sub-micrometer range under optimized process parameters. If such a high resolution is not required, a slightly thicker resist from this series (for example AZ® ECI 3027) can be useful. If thinner resist layers are required, we recommend AZ® ECI 3007, or alternatively a dilution of AZ® ECI 3012 with PGMEA = AZ® EBR Solvent. For applications with high requirements for very good resist adhesion, such as wet etching and galvanic deposition, we recommend resists from the AZ® 1500 or 4500 series.
Developers
For development, we recommend either TMAH-based developers such as AZ® 326 MIF, or 726 MIF, the NaOH-based AZ® 351B, and if the requirements for selectivity are not too high, the KOH-based AZ® 400K. with AZ® 351B or AZ® 400K, it may be advisable to work with a higher diluted developer (for example 1:5 to 1:6) instead of the usual 1: 4 dilution to achieve very fine resist structures or better controllable development times. On alkaline-sensitive substrate materials such as aluminum, we recommend the aluminum-compatible AZ® Developer in a 1:1 dilution.
Removers
If the resist structures have not been thermally cross-linked by plasma processes, ion implantation or high temperatures (> approx. 140 °C), all common removers such as AZ® 100 Remover, DMSO or many other organic solvents (e.g. acetone rinsed with isopropanol) are suitable for removing the resist layer. For cross-linked resist structures, high-performance strippers such as the NMP-free TechniStrip P1316 or AZ® 920 Remover, are recommended, and in the case of alkaline-sensitive substrate materials (such as aluminum), the TechniStrip MLO 07.
Thinning/ Edge Bead Removal
PGMEA = AZ® EBR Solvent can generally be used as a thinner for spin coating, which can also be used to remove edge ridges if necessary.
Further Information
Our safety data sheets and some of our technical data sheets are password-protected.
You will receive the access data after completing the form.
The access data for the data sheets are not your login data from our shop!
MSDS:
Safety Data Sheet AZ® ECI 3012 Photoresist english
Safety Data Sheet AZ® ECI 3012 Photoresist german
TDS:
Technical Data Sheet AZ® ECI 3012 Photoresist english
Technical Data Sheet AZ® ECI 3000 Series english
Application Notes:
Further Information about Photoresist Processing
Related products
Developer
Remover