AZ 4562 Photoresist - 3.785 l
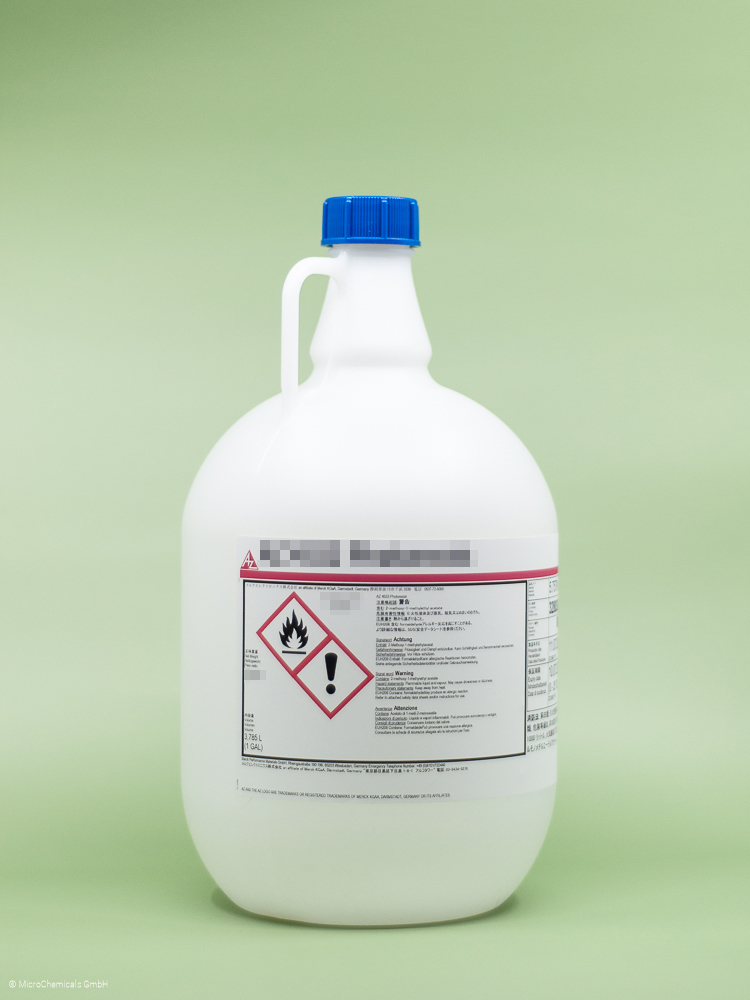
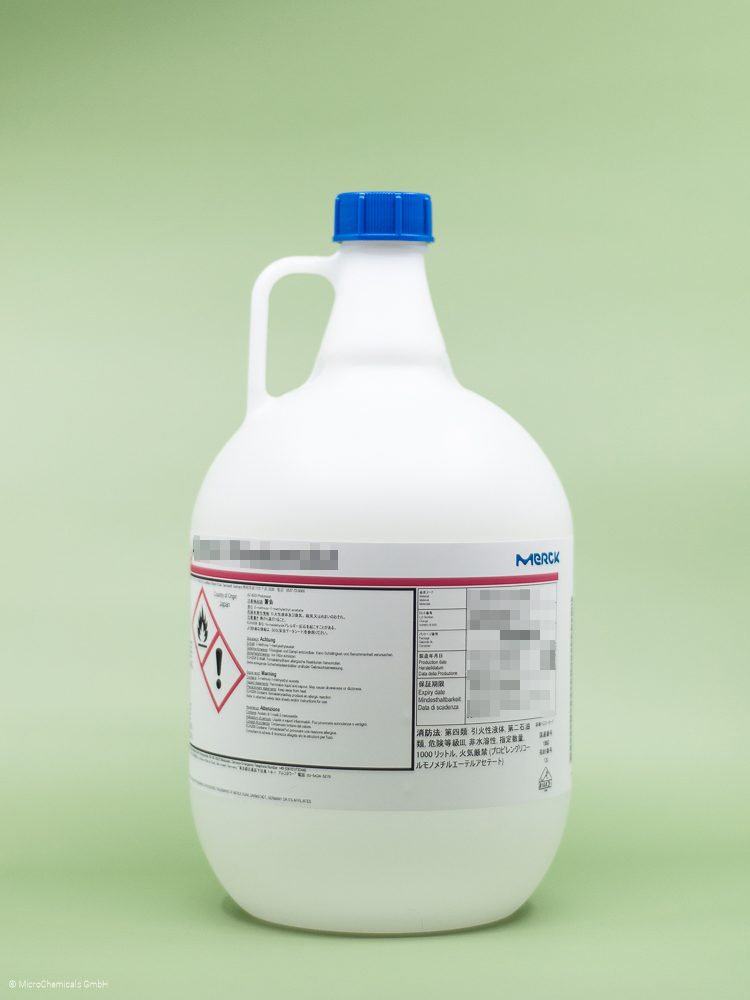
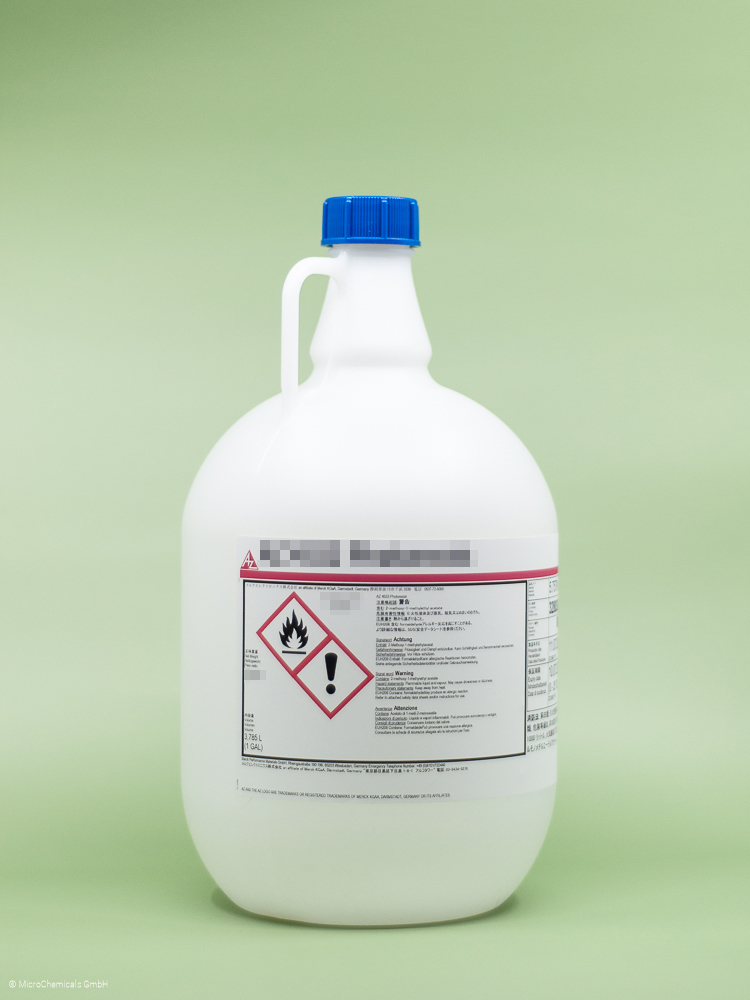
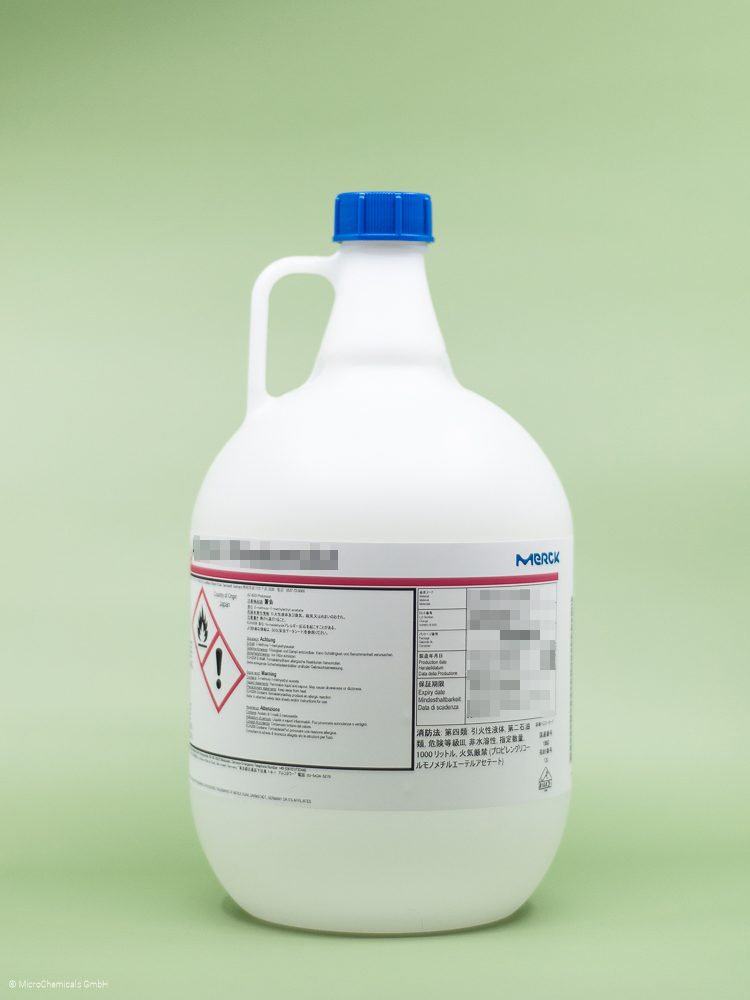
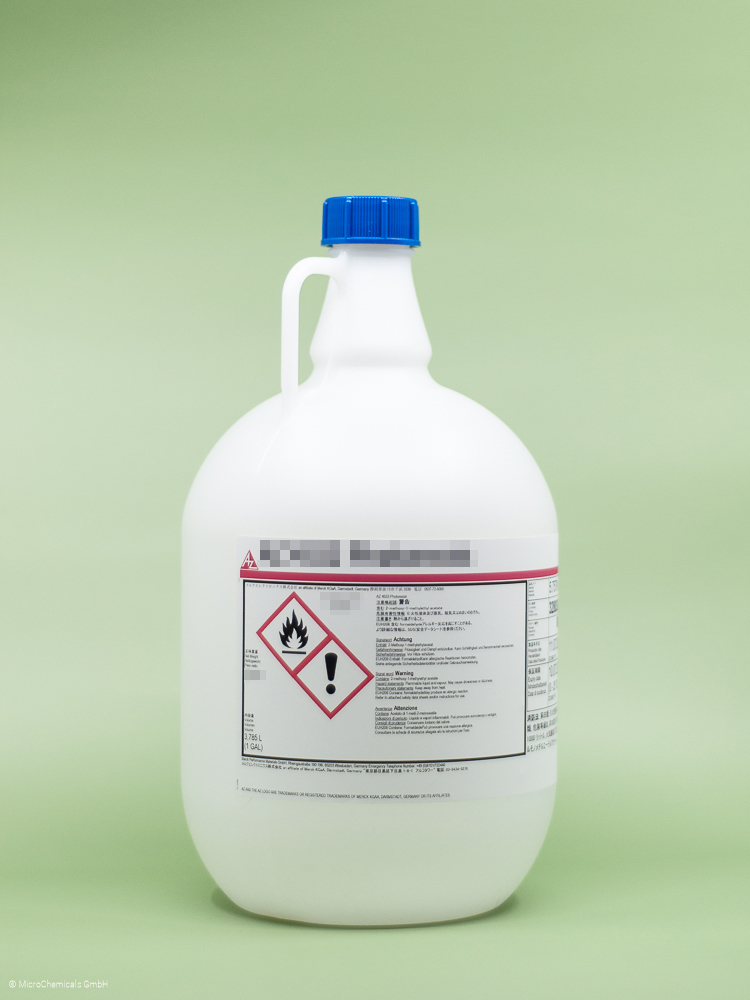
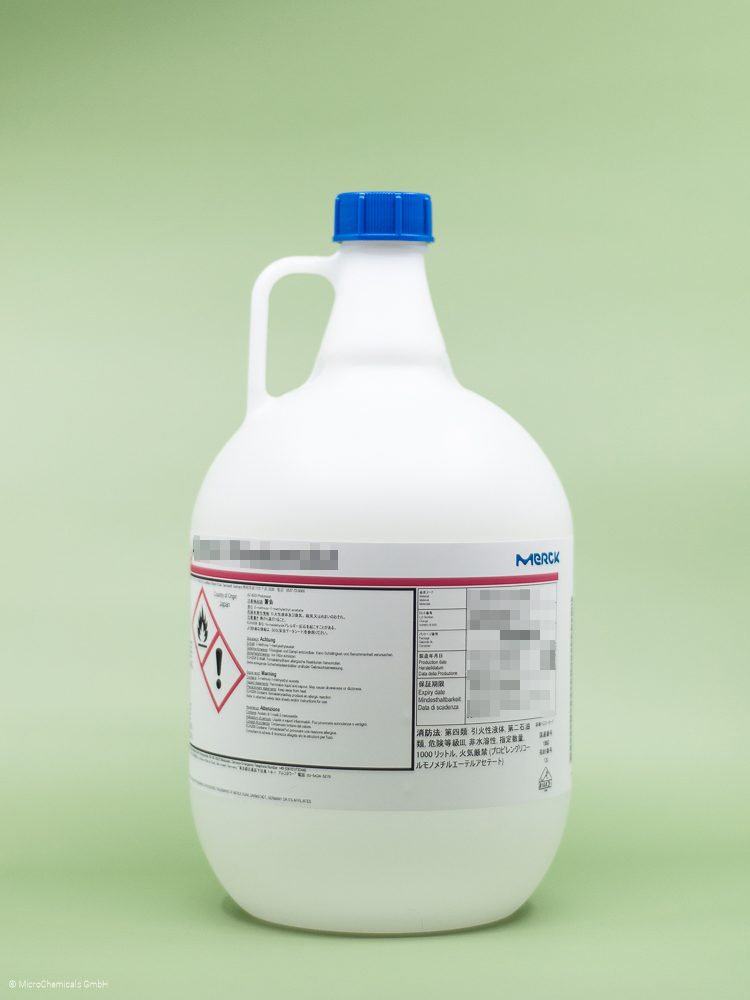
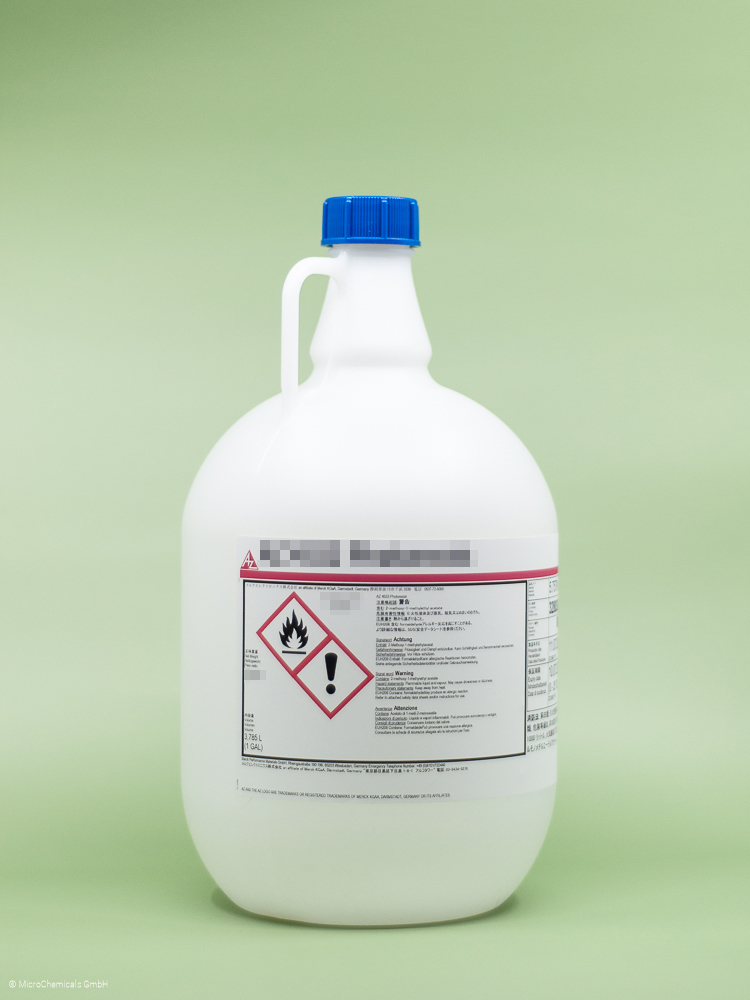
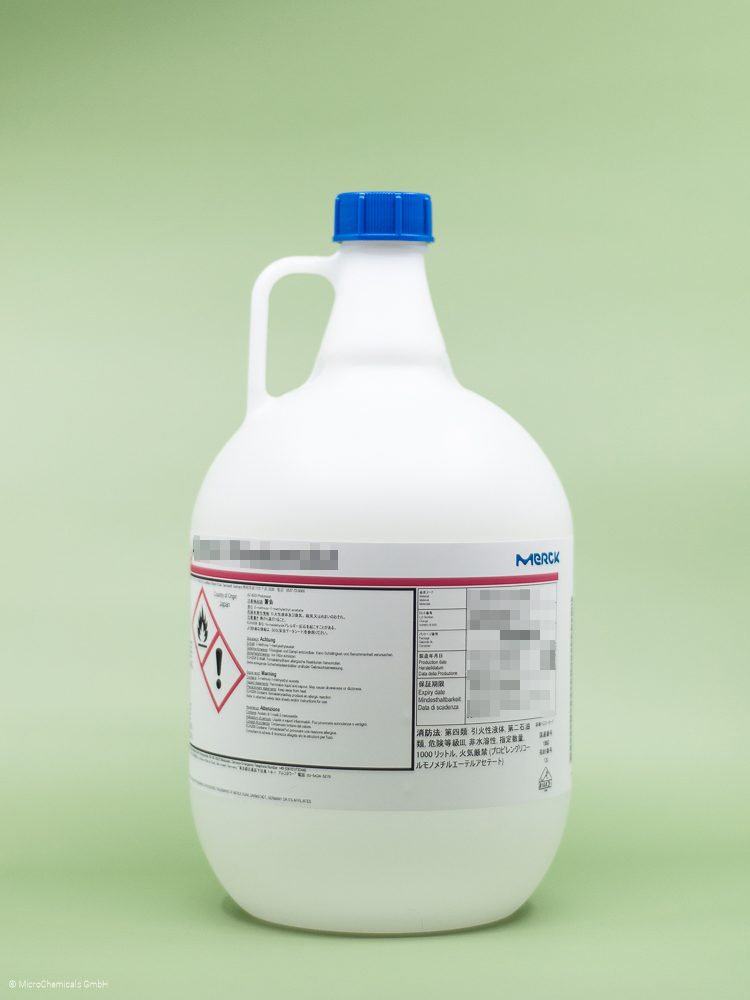
Product information "AZ 4562 Photoresist - 3.785 l"
AZ® 4562
Thick Resists with Optimized Adhesion
General Information
AZ® 4562 belongs to the AZ® 4500 series of positive resists (g-, h- and i-line sensitive) in the medium to high resist film thickness range, the main application of which is as a resist mask for wet etching or electroplating.
Product Properties
AZ® 4500 resist family is not optimized for very steep resist sidewalls nor for high stability against thermal softening (softening temperature approx. 100 °C), but rather for very high adhesion to all common substrate materials. The low photoinitiator concentration of the AZ® 4500 series resists compared to thin resists (such as the AZ® 1500 series) allows the exposure of even thicker resist layers without the risk of nitrogen bubbles forming in the resist layer.
AZ® 4562 is often used in electroplating or for etching metallic or non-metallic layers. AZ® 4562 achieves a resist film thickness of approx. 6 µm at a spin speed of 4000 rpm. With an appropriately adjusted spin profile, the resist film thickness range of approx. 4.5 - 20 µm can be covered. If thinner resist films are required, the AZ® 4533 is recommended, which differs from the AZ® 4562 only in the higher solvent content. From approx. 10 µm, processing the AZ® 4562 becomes increasingly time-consuming: the soft bake and subsequent development take longer, rehydration between the soft bake and exposure requires more and more time, and there is also the risk of nitrogen bubbles forming during exposure. For resist film thicknesses greater than 10-20 µm, it is recommended to consider using a chemically amplified thick resist such as AZ® 12 XT (5 -20 µm resist film thickness) or IPS 6090 (> 20 µm resist film thickness), which have significantly shorter softbake and development times at the corresponding resist thickness and do not require rehydration and significantly lower exposure doses.
Developers
For development, we recommend either TMAH-based developers such as the ready-to-use AZ® 326 MIF or 726 MIF, or the KOH-based AZ® 400K (typically 1:4 diluted with water, for faster development also slightly stronger with 1:3.5 or 1:3). On alkaline-sensitive substrate materials such as aluminum, we recommend the aluminum-compatible, undiluted AZ® Developer.
Removers
If the resist structures have not been thermally cross-linked by plasma processes, ion implantation or high temperatures (> approx. 140 °C), all common removers such as AZ® 100 Remover, DMSO or many other organic solvents (e.g. acetone rinsed with isopropanol) are suitable for removing the resist layer. For cross-linked resist structures, high-performance strippers such as the NMP-free TechniStrip P1316 or AZ® 920 Remover are recommended, and in the case of alkaline-sensitive substrate materials (such as aluminum), the TechniStrip MLO 07**.
Thinning/ Edge Bead Removal
If the resist is to be diluted for spin coating, PGMEA = AZ® EBR Solvent is the recommended solvent. PGMEA is the solvent for AZ® 4562 anyway and is also recommended for edge removal if necessary.
Further Information
Our safety data sheets and some of our technical data sheets are password-protected.
You will receive the access data after completing the form.
The access data for the data sheets are not your login data from our shop!
MSDS:
Safety Data Sheet AZ® 4562 Photoresist english
Safety Data Sheet AZ® 4562 Photoresist german
TDS:
Technical Data Sheet AZ® 4562 Photoresist english
Application Notes:
Further Information about Photoresist Processing
Related products
Developer
Remover